Зробимо короткий огляд холодильної системи, яку компанія НІО «Холод» розробила для замовника з України.
Об’єкт вже майже повністю змонтований та вводиться в експлуатацію.
Як для України, це без сумніву великий проєкт, і хочеться побажати всім нам щоб у нас в країні будувалось більше підприємств подібного масштабу.
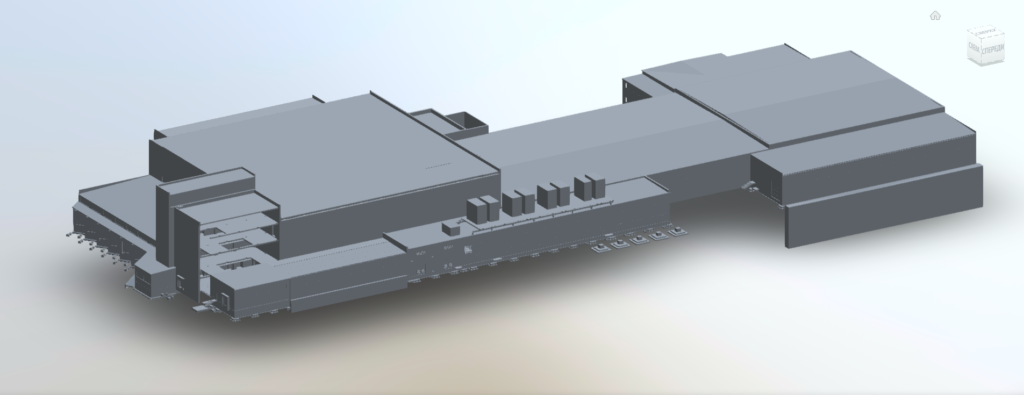
Для початку, відкрию модель будівлі. Площа тільки машинного відділення більш ніж 500 м.кв., а площа охолоджуваних приміщень близько 12,5 тис.м.кв. Серед споживачів холоду три поверхи холодильника з камерами зберігання охолодженої та замороженої продукції, виробничі приміщення, коридори та експедиції а також декілька морозильних апаратів.
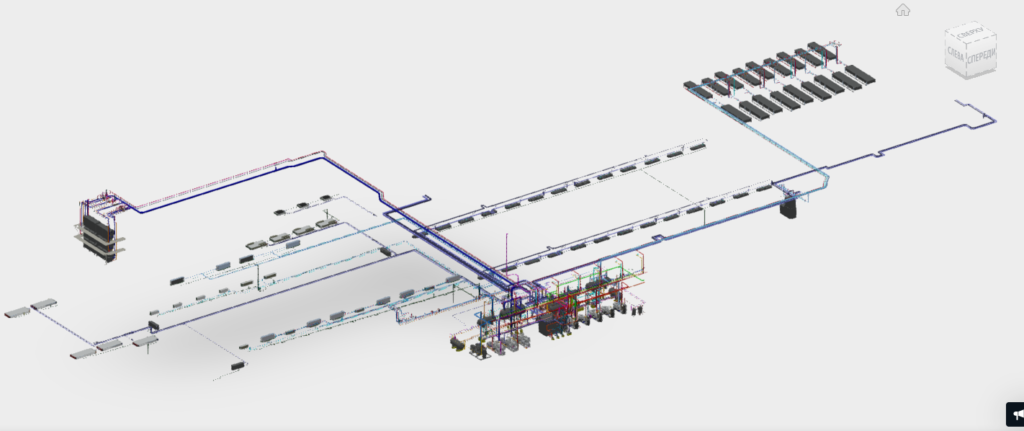
Для наглядности, тепер залишимо тільки модель трубопроводів, тут ми бачимо:
- Виробниче приміщення, що охолоджуется проміжним холодоносієм.
- Камера крапельного охолодження де продукт рухається вздовж підвісних шляхів, та охолоджується завдяки інтенсивному обдуву а ще зрощенню крижаною водою. Крижану воду ми доречі отримуємо у плівковому охолоджувачі.
- Окремо варто звернути увагу на камеру шокової заморозки, де в три поверхи встановлені шокфростери Термофін які виконані на спецзамовлення, кожен холодовиданистю під 250 кВт, а загальна висота конструкції більш ніж 7 метрів.
Якщо говорити про ситему в цілому, для статистики, я звів у табличку декілька узагальнюючих цифр
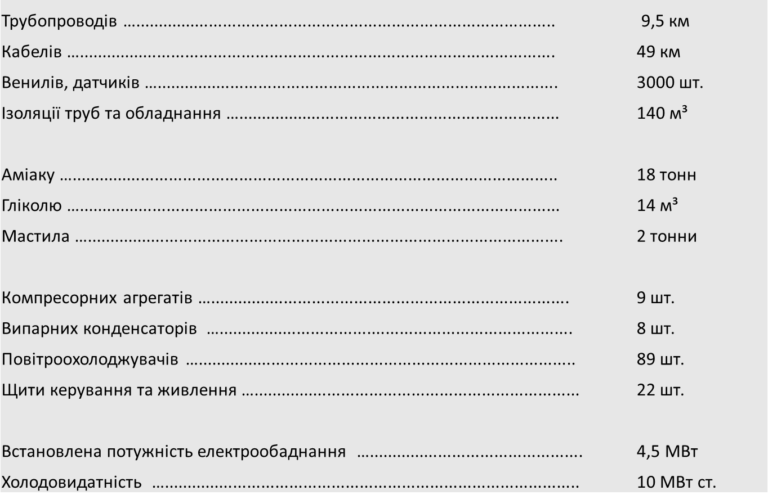
Пару слів про систему керування
Сигнали з датчиків та приладів керування надходять на модулі вводу виводу локального щита.
Такі щити розташовані безпосередньо біля технологічних ділянок, наприклад – це кожен поверх холодильника, або технологічна ділянка.
Потім, сигнали збираються та передаються по протоколу PROFINET до щитової, де стоїть головнийй контролер. Таким чином, на нього приходять сигнали з 65 модулів розширення а також, ETHERNET кабелю, данні з 9 пультів керування компресорами GEA Omni.
Далі по MODBUS зведені данні віддаються на комп’ютер на робочому місці оператора.
Загалом, для керування системою було зібрано 22 щіти з понад 5 тис. деталей.
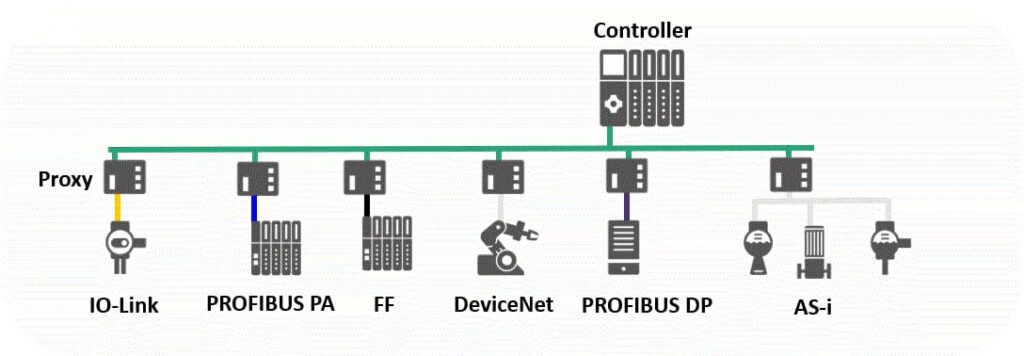
Розглянемо більш детально компресорне відділення
Так виглядає принципова схема частини системи що знаходиться у компресорному відділенні:
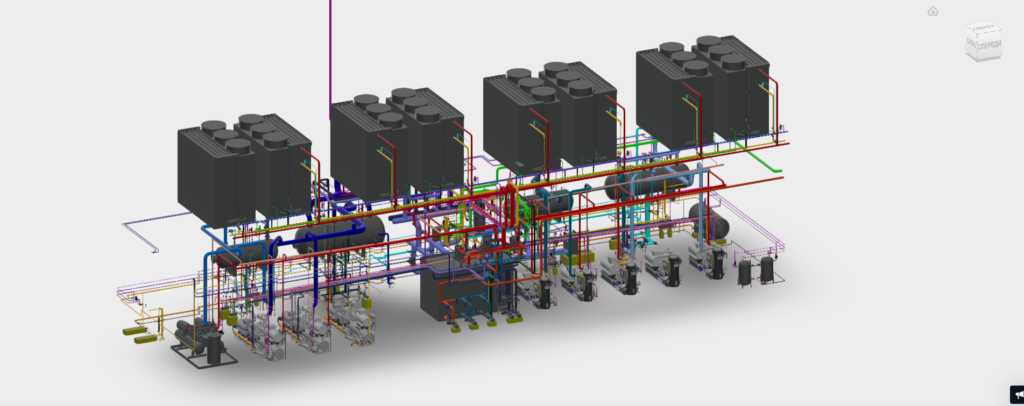
Система підтримує 4 рівні температури кипіння
це мінус 41˚С
мінус 29˚С
мінус 9˚С
мінус 4˚С
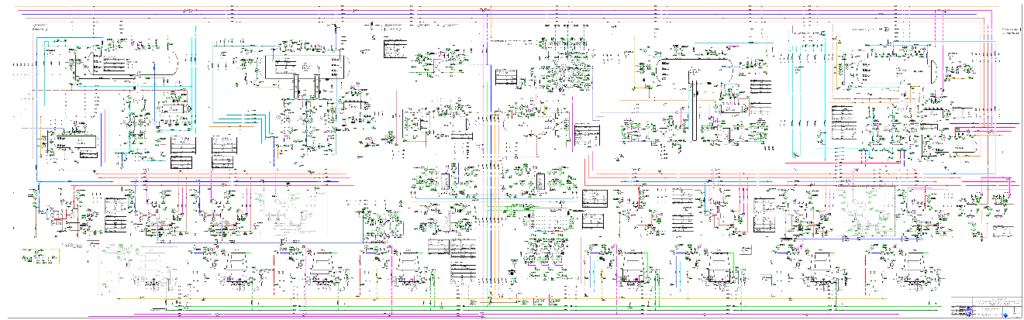
4 двохступеневих, та 5 одноступеневих гвинтових компресорних агрегати виробництва GEA Grasso нагнітають пари аміаку в спільний колектор.
Ним, пари потрапляють або безпосередньо у випарні конденсатори, або попередньо проходять через теплообмінники утилізації теплоти форконденсації, це дозволяє гріти воду для системи опалення або для потреб підприємства в об’ємі 50 кубів на годину.
Трубопроводи зливу рідкого аміаку з конденсаторів облаштовани системою очищення від неконденсованих газів.
Чим неконденсоані гази (а це здебільшого повітря) шкідливі для системи, можете почитати у нас на сайті
Лінійні ресивери у собі поєднують функцію термосифону для охолодження системи масла гвинтових компрессорів.
На низькотемпературних компресорних аппаратах ми доречі також утилізуємо теплоту мастила і робимо це через окремий гідравлічний контур щоб не забруднити тепообмінники компресорів.
Рідкий аміак що йде на дросилювання ми переохолоджуємо у пластинчастому теплообміннику за допомогою холодної води з водопроводу підприємства, яку далі використовуємо для поповнення випарних конденсаторів які у піку потребують до 25 м3 води на годину.
Перша ступінь дросилювання проходить паралельно у дев’яти кубовий циркуляційний ресивер систем мінус 4, та у 12 кубовий ресивер системи мінус 9, який також виконує роль проміжної посудини, бо далі з нього рідкий аміак надходить на дросилювання у найбільшу ємність, це аж у 18и кубовий ресивер системи -41.
Розподілення амміаку з ресиверів -41, -29, та -9 до приладів охолодження виконується за допомогою герметичних насосів, а на ресивері -4, для охолодження пропіленглікою, виконана гравітаційна схема з двома затопленими теплообмінниками.
Тож, щоб узагальнити, давайте ще раз перелічу технічні рішення які ми впровадили в рамках однієї системи
- Двоступеневе стиснення парів
- Утилізація теплоти форконденсації
- Утилізація теплоти масла
- Поділення контурів теплоносія на умовно брудний та чистий
- Відтаювання гарячою парою
- Переохолодження рідкого аміаку
- Гравітаційна та насосні схеми подачі холодоагенту
- Двоступеневе дросилювання
- Термосифонне охолодження мастила,
- Система очищення від неконденсованих газів
Кожне з цих рішень позитивно вливає на енергоефективність або на надійність системи, та цілковито виправдане з точки зору окупності.